Corso
1925
Set Up Hours of Automation with Load Trays and Accumulation Tables
The Feedall line of accumulation tables, load tables, and load trays is collectively represented by the Corso 1925 model. This automation equipment is designed to collect, hold, and feed products between different production stages, with a primary function of managing the flow of parts—acting as a buffer to handle discrepancies in production speeds between sections of a production line.
These tables temporarily store products in a non-specific orientation, allowing for a continuous flow of items even if downstream processes are slower or momentarily stopped. They are essential to balancing line flow and are companion components to critical CNC machining cells that rely on a steady stream of parts for efficiency.
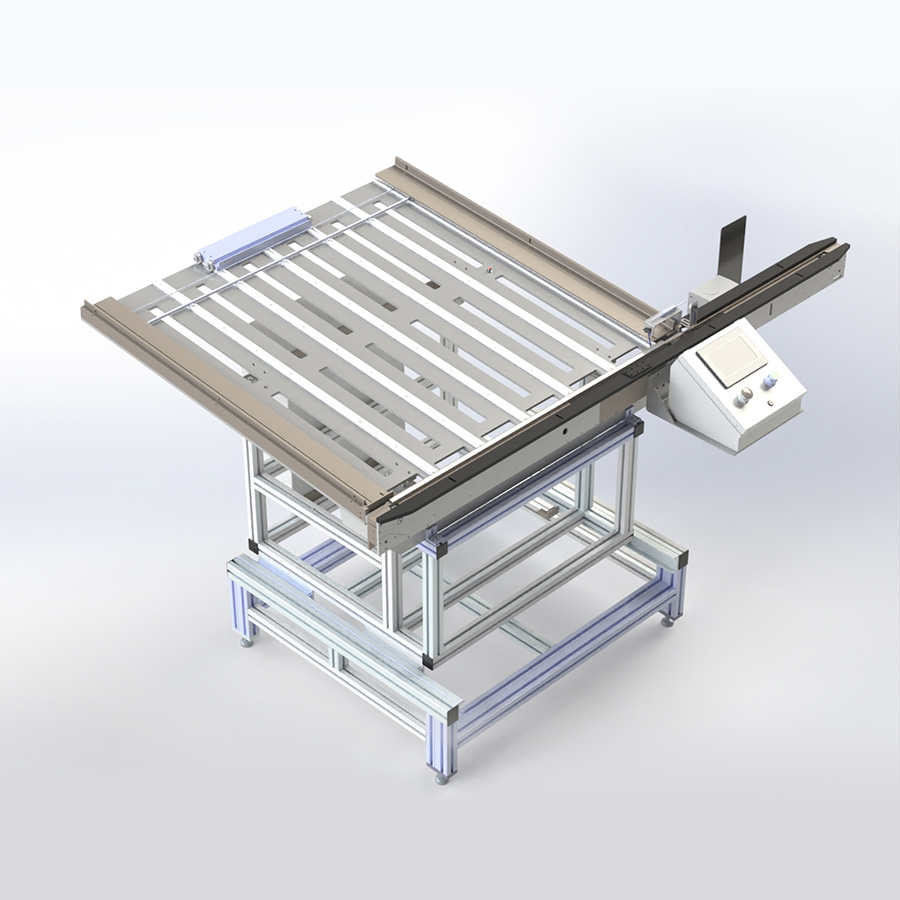
Overview
The Corso 1925 provides a cost-effective tool to keep parts supplied for CNC machine loading or conveyors, and serves well in buffer applications between machines to maximize uptime. It helps prevent bottlenecks and ensures that upstream processes can continue operating efficiently without interruption.
The flexibility provided by accumulation tables and load trays to design creative solutions is also enchanted by Feedall’s customization options and expertise across a wide range of automation equipment.
We work with you on the table layout and design, making sure they are created with your CNC machine cells and available floor space in mind. For example, we can provide large dimension accumulation tables that can hold hundreds of pounds of parts providing hours of uninterrupted workpieces for the machine tending robots. We can also design highly customized load trays specific to certain parts that hold workpieces securely in place, ideal for transporting and precisely presenting complex parts for CNC machining.
The Corso 1925 is easily adjusted for various part sizes and ideal for systems that have variable feed rates between two operations, and can buffer up 1-2 hours of parts leaving downstream operations to continue working at a fixed feed rate. For more details, please contact our team of automation experts.